By Frank Esposito SENIOR STAFF REPORTER Published: October 14, 2014 12:44 pm ET Updated: October 14, 2014 12:51 pm ET
Image By: Caroline Seidel Mark Beitz, vice president styrenic specialties, at Styrolution GmbH's booth at Fakuma 2014.
FRIEDRICHSHAFEN, GERMANY — Styrolution GmbH has added production capacity at plants in the U.S. and Germany and is promoting the merits of its transparent styrenic resins.
Frankfurt, Germany-based Styrolution recently began making NAS-brand styrene methyl-methacrylate (SMMA) resins at its plant in Decatur, Ala. The firm had made that material in Indian Orchard, Mass., until closing its plant there earlier this year.
In Ludwigshafen, Germany, Styrolution this month launched production of NAS and of Zylar-brand styrenic copolymers at a unit that previously had made ABS and ASA resins. The Ludwigshafen site has annual capacity of about 25 million pounds. No SMMA capacity number for Decatur was available.
Previously, Indian Orchard had been Styrolution’s only global NAS production site.
“Customers want supply flexibility, so it’s important to have a backup plan by having two facilities,” Mark Beitz said Oct. 14 at Fakuma in Friedsrichshafen. Beitz serves as Styrolution’s vice president of business management for styrenic specialties in Europe, the Middle East and Africa.
On the new product side, Styrolution has launched new grades of Zylar and of its Clearblend-brand styrene acrylic copolymer. Both grades are transparent, but remain strong with good impact strength, officials said.
“We have the best clarity you can get,” Beitz said, “along with good chemical resistance, high flow and short cycle times.”
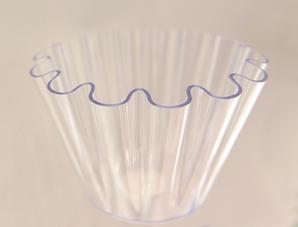
Image By: Caroline Seidel Styrolution says its customers are seeking more clear resin choices.
The new grades are being used in products ranging from refrigerator drawers to water filters. Other applications include toys, appliances, office accessories and consumer goods.
So far in 2014, Beitz said that Styrolution’s customers have been mostly optimistic, in spite of low economic growth in the U.S. and a flat economy for Europe. “They’re willing to try new things,” he added. “Medical is growing and automotive and household are doing OK.”
Other applications focused on by Styrolution at Fakuma include:
• The AxoTrack vascular access system, a virtual needle technology from Soma Access Systems of Greenville, S.C. This real-time needle tracking system uses Zylar-brand styrenic copolymer.
• White medical tubes that act as stabilizers for filter elements from Microspec Corp. of Peterborough, N.H. The tubes use Styroflex-brand styrenic copolymer.
• An HPV (human papillomavirus) sampler to detect cervical cancer and other illnesses from Delphi Bioscience of Scherpenzeel, the Netherlands. The sampler uses Novadur-brand ABS.
• The EZ Trocar surgical tool — which allows surgical instruments to be introduced into the chest and abdominal cavities — from Hakko Corp. of Osaka, Japan. The trocar uses Terlux-brand methyl methacrylate ABS.
Styrolution officials said that all of these materials offer a combination of aesthetics and functionality. “Every day, our styrenics specialties unlock new possibilities and enable innovative application breakthroughs for customers across an array of industries,” Europe/Middle East/Africa region president Kevin McQuade said in a news release.
In 2013, Styrolution posted sales of 5.8 billion euros (US$7.5 billion). The firm employs 3,200 at 17 sites worldwide.
Styrolution was formed in 2011 as a styrenics joint venture between German plastics and chemicals giant BASF SE and Swiss materials maker Ineos Group. In June, Ineos announced that it would buy out BASF’s 50 percent stake in Styrolution by the end of the year.
|